Categories
- 10 Best Bod Incubator 2025 at Lowest Price
- 10 Best Compound Microscopes 2025 at Lowest Prices
- 10 Best Lab Chemicals 2025 at Lowest Prices
- 10 Best Lab Equipment Suppliers 2025 - Lowest Prices Available
- 10 Best Lab Microscopes 2025
- 10 Best Microbiology Lab Equipment 2025 at Lowest Prices
- 10 Best Refrigerator Mortuary Freezer India
- 10 Best Student Microscopes 2025 at Lowest Prices
- 10 Best Vertical Autoclaves 2025 - Vertical Autoclaves Best Prices 2025
- Accessories Collection: Trendy and Essential Items
- Aerospace Engineering Equipment Collection for Optimal Research and Innovation
- Agriculture Lab Equipment for Precision Farming and Research
- Agriculture Lab Equipment Suppliers for Agriculture College Needs
- Agronomy Lab Equipment for Precise Agricultural Research
- analytical lab equipment for precision testing and research
- Anatomy Lab Equipment Collection for Education and Research
- Animal House Lab Equipment: Essential Tools for Research
- AUTOMOBILE LAB: Explore Innovations in Automotive Engineering
- ayurvedic drug testing laboratory for quality assurance and effectiveness
- Ayurvedic Lab Equipment Suppliers and Manufacturers for Colleges
- Ayurvedic Pharmacy Instruments: Essential Ayurvedic Pharmacy Tools
- B Pharmacy Equipment Suppliers: Quality Supplies for Your Pharmacy
- B. D. Instrumentation India: Leading Solutions in Instrumentation
- Best Microscope for Students in India: Top Picks for Students
- Binocular Microscope Collection
- Biochemistry lab equipment
- Biological Lab Equipment Collection
- Biological Lab Equipment for Research and Experimentation in Biological Sciences
- Biology Lab Equipment
- Biomedical Engineering Lab Equipment
- Biophysics Lab Equipment for Research and Experiments - Essential Tools for Biophysics Studies
- Biostatistics Lab Equipment
- Biotechnology Collection: Innovative Advances in Biotechnology
- Biotechnology Lab Tools and Equipment for Advanced Research
- Biotechnology Lab Tools for Efficient Research and Innovation
- Borolab Scientific Glass Pvt. Ltd.
- Botany Lab Supplies for All Your Plant Research Needs
- Botany Permanent Micro-Prepared Slides Collection - Botany Micro-Prepared Slides
- CAD Lab Collection - Innovative Designs and Solutions
- Cardiology Lab Equipment
- Central Drug House Collection - CDH
- CENTRAL WORKSHOP Collection: Premium Tools and Equipment for Every Project
- Centre for Community Medicine Lab Equipment Collection
- Centrifuge Machine Collection: Explore Top Models and Features
- Centrifuge Machine Suppliers India - Quality and Reliability at Its Best
- Chemical Engineering Equipment Collection
- Chemistry equipment
- Chemistry Lab Apparatus - Essential Chemistry Lab Equipment
- Chromatography Apparatus Collection for Efficient Separation Techniques
- Civil Engineering Collection: Essential Resources and Insights
- Clean Air Equipment
- College of Nursing Lab Equipment
- D Pharmacy equipment
- Dairy Analysis Instruments: Essential Tools in the Dairy Lab Collection
- Dental Autoclave Cost and Price Analysis Collection
- Dental Equipment Supply and Tools for Professionals
- Department of Anatomy Lab Equipment – Essential Anatomy Lab Equipment for Students and Professionals
- DEPARTMENT OF P'CEUTICAL CHEMISTRY Equipment - Pharmaceutical Chemistry Equipment
- DEPARTMENT OF P'CEUTICS Equipment - Pharmaceutical Equipment Collection
- DEPARTMENT OF PHARMACOGNOSY Equipment - Essential Tools for Research and Analysis
- DEPARTMENT OF PHARMACOLOGY Equipment
- Diffusion Cell Apparatus: Understanding Its Applications and Benefits
- Digital Centrifuge Machine Collection
- Distillation Equipment: Essential Distillation Apparatus for Your Collection
- Do Meter Collection: Unique Designs and Innovative Styles
- DYNAMICS OF MACHINES LAB: Comprehensive Resources for Understanding Machine Dynamics
- EDM LAB Equipment Collection: Essential EDM LAB Equipment for Your Needs
- Endocrinology Lab Equipment for Metabolism & Diabetes Research
- Engineering Institute Laboratory Equipment Collection - Engineering Laboratory Equipment
- Engineering Laboratory Equipment Collection: Essential Instruments and Tools
- ENT and Ophthalmic Conditions Collection
- Entomology Lab Equipment Essentials
- Flash Point Apparatus Collection for Accurate Testing
- Fluid Mechanics Lab Collection: Machinery Fluid Lab Experiments
- FMS LAB Collection - Explore Unique Innovatives
- Gastroenterology and Human Nutrition
- General Laboratory Equipment Collection for Efficient Research
- General Laboratory Equipment for Accurate Experiments and Analysis
- Genetics and Plant Breeding Equipment for Your Lab Needs
- Genetics and Plant Breeding Equipment: Essential Lab Tools for Research
- Haematology Lab Equipment: Essential Haematology Lab Instruments
- Handi Centrifuge Machines Collection
- Heart Models Collection: Unique Designs and Inspirations
- HEAT & MASS TRANSFER LAB
- Heating and Cooling Solutions for Optimal Comfort with Laboratory Equipment
- Herbal Products Quality Analysis in Herbal Testing Laboratory
- High-Quality Laboratory Equipment by Glomax - Leading Laboratory Equipment Manufacturer
- Hospital Equipment for Healthcare Professionals Collection
- Hospital Equipment Supplier Near Me: Your Local Source for Quality Medical Supplies
- Human Body Part Models Collection
- Human Skeleton Model - White PVC Plastic Educational Tool
- I.C. Engine Technology: Comprehensive Insights and Experiments in Internal Combustion Engine Lab
- Industrial Soil Equipment Collection: Essential Tools for Soil Management
- Kashmir Surgical Works - Quality Kashmir Surgical Instruments
- Knee Joint Model Collection
- Lab Chemicals: Essential Lab Chemical Supplies for Your Experiments
- Lab Equipment Collection: Essential Tools for Every Laboratory
- Lab Fabric Items Collection: Unique and Versatile Designs
- Lab Plasticware Supplies Collection for Laboratory Equipment and Supplies
- Lab Water Bath Collection: Essential Equipment for Precision Heating
- Laboratory Centrifuge Collection: Explore Top Laboratory Centrifuge Solutions
- Laboratory Consumables and Essential Laboratory Supplies
- Laboratory Equipment Collection: Essential Tools for Science and Research
- Laboratory Equipment Collection: Essential Tools for Your Experiments
- Laboratory Equipment Suppliers Ambala Cantt - Quality & Variety Available
- Laboratory Equipment Suppliers and Manufacturers Collection
- Laboratory Equipment Suppliers Delhi: Top Providers in the Capital
- Laboratory Equipment Suppliers India: Your Trusted Source
- Laboratory Equipment Suppliers Jaipur: Top Providers in the City
- Laboratory Equipment: Essential Tools for Every Laboratory
- Laboratory Glassware and Chemicals for Your Collection
- Laboratory Instruments Manufacturers Ambala Cantt
- Labpro Banner 60% Collection
- Labpro Banner Collection - Elevate Your Space with Unique Designs
- Labpro international
- Live Stock Management Equipment for Production Management Lab
- Livestock Production Management: Strategies for Effective Livestock and Production Management
- MATERIAL SCIENCE LAB - Explore Innovations in Material Science Lab
- Measurement and Metrology Lab Collection
- Measuring Tools for Precision: Accurate Measurements and Precision
- Mechanical Engineering Techniques: A Comprehensive Collection
- Medical laboratory equipment suppliers
- Medical Mannequin Collection for Training and Education
- Medical Supplies and Products Collection
- Mega Offers Discounts: Unbeatable Deals and Discounts Collection
- Melting Point Apparatus Collection
- Metrological Lab Equipment for Accurate Measurements and Testing
- Microbiological Diagnostic Equipment for Accurate Testing
- Microbiology and Pharmacology Equipment Collection
- Microbiology Laboratory Equipment and Zoology Lab Equipment
- Microcentrifuge Collection: Essential Tools for Precision Lab Work
- Micrometer: Explore Our Unique Micrometers Collection
- Micropipettes for Lab Use Collection
- Microscopes for Tiny Details: Explore the World of Tiny Details
- Milk Testing Equipment Collection: High-Quality Solutions for Accurate Results
- Mushroom Lab Equipment for Cultivation and Research
- Nephrology Lab Equipment: Essential Tools for Renal Research
- Nursing Lab Equipment Collection for Nursing College
- Nursing Lab Equipment for Nursing Department Collection
- Obstetrics and Gynaecology Equipment for Enhanced Care in Lab Settings
- Offer Zone: Exclusive Deals and Discounts Collection
- Orthopaedics Lab Equipment Collection
- OSAW Industrial Products Pvt Ltd - Quality Industrial Solutions
- Otorhinolaryngology Lab Equipment Collection
- Paediatrics Lab Equipment for Accurate Diagnosis and Care
- Pathology Lab Equipment for Accurate Diagnostics
- Pediatric Lab Equipment: Essential Tools for Child Healthcare
- PERMANENT SLIDES Collection for Lasting Impact
- pH meters for research - Top-Rated pH Meters for Accurate Testing
- Pharma Analysis Equipment for Laboratory Use
- Pharma Lab Equipment Collection for Enhanced Research Productivity
- Pharmaceutical and Research Lab Equipment Collection
- PHARMACEUTICAL BIOTECHNOLOGY EQUIPMENT
- Pharmaceutical Chemistry Lab Equipment Collection
- Pharmaceutics Laboratory Equipment Collection
- Pharmacognosy Lab Equipment Collection
- Pharmacology Lab Equipment: Essential Pharmacology Lab Tools
- Pharmacy Lab Equipment Suppliers for Quality Pharmacy College Tools and Supplies
- Pharmacy Laboratory Equipment Collection
- Physical Pharmacy Physics Lab Equipment Collection
- Physics Discount Items - 60% Off Select Products
- Physics Lab: Engaging Physics Lab Experiments for All Levels
- Physiology Lab Equipment for Essential Experiments
- Plant Pathology Microbiology Lab Collection
- product Offers 2024
- Profile Projectors: Precision Measurement Tools for Accurate Profile Analysis
- Pusher Centrifuge Collection: Innovative Solutions for Efficient Separation
- RADICAL SCIENTIFIC EQUIPMENTS PVT LTD - Radical Scientific Equipment Collection
- Refrigerated Centrifuge Suppliers and Manufacturers Collection
- REFRIGERATION & AIR CONDITIONING LAB
- Reproductive Biology lab equipment
- Research Section Lab Equipment - Essential Research Lab Equipment for Your Needs
- Rheumatology Lab Equipment and Rheumatology Lab Supplies
- Rheumatology Lab Tools for Accurate Diagnosis and Efficient Testing
- School and College Equipment Collection
- School and College University Products Collection for All Your Needs
- school lab equipment manufacturers in india
- Science Laboratory Equipment Collection for All Your Needs
- Scifa Laboratory Equipment: Innovative Solutions for Your Lab Needs
- SCITECH SCIENTIFICS: Advancing Scitech Scientific Research
- Seed Technology Collection: Innovations in Seed Technology
- Seed Technology Lab Equipment for Advanced Seed Technology Equipment Solutions
- Silica Gel Collection: Unique and Versatile Silica Gel Products
- Skull Models Collection: Unique and Intricate Designs
- Soil Testing Instruments Collection
- soil testing lab equipment list
- Soxhlet Extraction Solutions for Efficient Solvent Extraction Apparatus
- Span Automation - Span Automation Solutions for Efficient Processes
- spectrophotometer
- Strength of Materials Lab: Unleashing Structural Integrity
- Table Top Centrifuge Collection: Premium Table Top Centrifuges for Precision Lab Use
- Testing Equipment Collection
- Tiles Ceramic Laboratory Equipment: Optimize Your Ceramic Laboratory Tiles Equipment for Effective Analysis
- Top Laboratory Fume Hood Manufacturers in India - Leading Laboratory Fume Hood Manufacturers India
- Types of Masks: Explore Various Types of Masks
- Types of Microscopes: A Comprehensive Guide to Different Microscope Types
- Urology lab equipment
- Veterinary Lab Products for Optimal Veterinary Sciences Lab Solutions
- Zoology Lab Equipment: Essential Zoology Lab Instruments
Recent Articles
Tag Cloud
Top Sellers
Process Control Equipment: Essential Tools for Effective Process Control Engineering
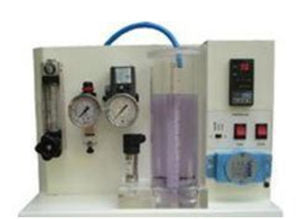
Process Control Equipment: Key Components in Engineering
Process control equipment plays a vital role in the effective management and optimization of industrial processes. In today's fast-paced technological environment, it is essential for engineers to have a comprehensive understanding of process control equipment. These tools aid in monitoring, controlling, and optimizing production processes, ensuring that they operate at peak efficiency while maintaining product quality and safety standards.
Process Control Engineering involves the use of various equipment and instruments to monitor and control industrial processes. Here are some commonly used equipment in process control engineering:
-
Programmable Logic Controllers (PLCs): PLCs are rugged industrial computers designed to automate and control manufacturing processes. They receive input signals from sensors, perform logical operations, and provide output signals to control actuators and devices. PLCs are highly versatile and can be programmed to perform complex control tasks.
-
Distributed Control Systems (DCS): DCS is a centralized control system used in large-scale industrial processes. It consists of multiple controllers distributed throughout the plant, interconnected via a communication network. DCS allows for centralized monitoring and control of various process parameters, such as temperature, pressure, flow rate, and level.
-
Supervisory Control and Data Acquisition (SCADA) Systems: SCADA systems are used to monitor and control industrial processes from a central location. They collect real-time data from remote devices and provide a graphical user interface for operators to visualize and control the process. SCADA systems often include features like alarm management, historical data logging, and reporting.
-
Human-Machine Interface (HMI): HMIs provide a graphical interface for operators to interact with process control systems. They display real-time data, control parameters, and provide status indicators. HMIs can be implemented using touchscreens, pushbuttons, and other input/output devices to facilitate efficient process monitoring and control.
-
Sensors and Transmitters: Various sensors and transmitters are used to measure physical parameters such as temperature, pressure, level, flow rate, and pH in industrial processes. These sensors convert the measured physical quantity into an electrical signal that can be interpreted by control systems. Common types of sensors include temperature sensors (thermocouples, RTDs), pressure transmitters, flow meters, and level sensors.
-
Actuators: Actuators are devices used to control or manipulate process variables. They receive control signals from the control system and convert them into mechanical action. Examples of actuators include control valves, motorized valves, solenoid valves, and variable frequency drives (VFDs) for controlling motor speed.
-
Data Historians: Data historians are software systems used to store and manage large amounts of historical process data. They provide long-term data storage, retrieval, and analysis capabilities, enabling engineers to analyze trends, perform optimization, and troubleshoot process issues.
-
Control Valves: Control valves are used to regulate the flow of fluids in a process. They receive control signals from the control system and adjust the valve position to maintain the desired flow rate or pressure. Control valves often incorporate actuators, positioners, and feedback mechanisms to provide accurate control.
-
Analytical Instruments: Analytical instruments are used to measure and analyze the chemical composition and properties of process fluids. Examples include pH meters, gas chromatographs, spectrometers, and moisture analyzers. These instruments provide valuable information for process optimization and quality control.
-
Communication Networks: Industrial process control systems rely on robust communication networks to exchange data between various devices and systems. These networks can be wired (Ethernet, fieldbus) or wireless (Wi-Fi, Zigbee), and ensure reliable and timely transmission of data for effective process control.
It's important to note that the specific equipment used in process control engineering can vary depending on the industry, process complexity, and specific requirements of the application.
LABORATORYDEAL India maintains a good quality assurance of all its products and provides lab equipment at affordable and eco-friendly rates. The company provides lab equipment throughout and outside the country and has a network of dealers and distributors in various states, including Andhra Pradesh, Arunachal Pradesh, Assam, Bihar, Chhattisgarh, Goa, Gujarat, Haryana, Himachal Pradesh, Jharkhand, Karnataka, Kerala, Madhya Pradesh, Maharashtra, Manipur, Meghalaya, Mizoram, Nagaland, Odisha, Punjab, Rajasthan, Sikkim, Tamil Nadu, Telangana, Tripura, Uttar Pradesh, Uttarakhand, and West Bengal
One key category of process control equipment includes sensors, which are instrumental in gathering data from the system. Sensors can measure various parameters such as temperature, pressure, flow rates, and levels of substances, providing real-time information that is crucial for making informed decisions. By analyzing the data collected from these sensors, engineers can identify trends, detect anomalies, and make necessary adjustments to maintain desired operational conditions.
Actuators also play a significant role in process control equipment. These devices are responsible for implementing control actions based on signals received from the control system. For example, actuators can adjust valves, change pump speeds, or modify equipment settings based on the data provided by sensors. The coordination between sensors and actuators forms the backbone of a robust process control system, allowing for precise control of various variables within a production process.
Another essential aspect of process control equipment is controllers, which receive input from sensors, analyze the data using pre-set algorithms, and send output signals to actuators to regulate process parameters effectively. Various types of controllers exist, including proportional-integral-derivative (PID) controllers, which are widely used for their simplicity and effectiveness. Understanding the different types of controllers and their applications is crucial for process control engineers working to optimize systems.
In addition to these primary components, process control equipment also includes control valves, which regulate the flow of liquids or gases within a system, and data acquisition systems, which collect and manage data from sensors for analysis. Integrating these devices into a cohesive process control strategy enhances operational efficiency, reduces waste, and improves product consistency.
Moreover, the implementation of advanced process control (APC) technologies can further elevate the performance of process control equipment. These technologies employ sophisticated algorithms to provide real-time optimization of process variables. By analyzing historical data and predicting future trends, APC systems can make proactive adjustments, helping to avoid inefficiencies and reduce the risk of production issues.
The benefits of effectively utilizing process control equipment extend beyond operational efficiency. Organizations can realize significant cost savings through reduced energy consumption, minimized downtime, and improved resource allocation. Additionally, maintaining a high standard of product quality protects a company's reputation, enhances customer satisfaction, and increases competitiveness in the market.
Training in the use of process control equipment is also vital for engineers and technical staff. Understanding how each component interacts within a system enables professionals to troubleshoot issues effectively and implement improvements. Continuous education and training programs ensure that teams remain proficient in using the latest technologies and practices in process control engineering.
In conclusion, process control equipment serves as the foundation of process control engineering, equipping professionals with the necessary tools to optimize industrial processes. By leveraging the capabilities of sensors, actuators, controllers, and advanced control technologies, engineers can ensure that operations run smoothly and efficiently, adhering to the highest standards of quality and safety.
Top Suppliers
Collections
- Dairy products
- Milk Testing Equipment
- physics lab
- Laboratory And Scientific Equi...
- microscopes
- ENT AND OPHTHALMIC
- measuring tools
- Centrifuge machine
- Micrometer
- Micropipette
- Silica Gel
- BOTANY PERMANENT MICRO-PREPARE...
- PERMANENT SLIDES
- centrifuge machine
- mask - type of mask
- medical products
- bod incubator
- Lab Chemical
- Do meter
- Lab Fabric items
- dental Autoclave
- medical mannequin
- White PVC Plastic Human Skelet...
- Human Body Part Models
- Heart Models
- Knee Joint Model
- Skull Models
- Laboratory Centrifuge
- Handi Centrifuges
- Microcentrifuge
- Table Top Centrifuge
- Digital Centrifuge Machine
- Pusher Centrifuge
- Laboratory Consumables
- Melting Point Apparatus
- Soxhlet Extraction Apparatus
- Distilling Apparatus
- Chemistry Lab Apparatus
- Chromatography Apparatus
- Diffusion Cell Apparatus
- Flash Point Apparatus
- Science Laboratory Equipment
- Profile Projectors
- Engineering Laboratory Equipme...
- Types of Microscopes
- General Laboratory Equipment
- Heating & Cooling Products
- Hospital equipment
- Testing Equipment
- Clean Air Equipment
- Engineering & Institute labora...
- HEAT & MASS TRANSFER LAB
- REFRIGERATION & AIR CONDITIONI...
- I.C. ENGINE LAB
- FLUID MECHANICS AND MACHINERY ...
- STRENGTH OF MATERIALS LAB
- EDM LAB equipment
- MATERIAL SCIENCE LAB
- FMS LAB
- CAD LAB
- AUTOMOBILE LAB
- MEASUREMENT & METROLOGY LAB
- DYNAMICS OF MACHINES LAB
- CENTRAL WORKSHOP
- Aerospace Engineering lab Equi...
- Biological Sciences lab Equipm...
- Chemical Engineering Equipment
- Civil Engineering
- Mechanical Engineering
- School And College University ...
- Lab Glassware & Chemical Items
- Zoology Lab Equipment
- Microbiology laboratory equipm...
- Chemistry Lab Products
- Botany Lab Product
- Biological Lab Equipment
- Department Of Anatomy Lab Equi...
- College of Nursing Lab Equipme...
- Endocrinology, Metabolism & Di...
- Haematology Lab Equipment
- Orthopaedics lab equipment
- Pediatric lab equipment
- Pathology lab equipment
- Physiology lab equipment
- Rheumatology lab equipment
- Urology lab equipment
- Obstetrics and Gynaecology lab...
- Otorhinolaryngology lab equipm...
- Pharmacology lab equipment
- Anatomy lab equipment
- Research Section lab equipment
- Pharmaceutical & Research Lab ...
- Physical Pharmacy Lab equipmen...
- Pharma Biology Laboratory Lab ...
- General Laboratory Equipment
- School And College University ...
- Medical College Lab equipment
- Biomedical Engineering Lab Equ...
- Biostatistics Lab Equipment
- Cardiology Lab Equipment
- College of Nursing Lab Equipme...
- Gastroenterology and Human Nut...
- Gastroenterology and Human Nut...
- Nursing Department lab equipme...
- Paediatrics lab equipment
- Reproductive Biology lab equip...
- Rheumatology lab equipment
- Biochemistry lab equipment
- Biophysics lab equipment
- Biotechnology lab equipment
- Centre for Community Medicine ...
- Nephrology lab equipment
- Pharmaceutical Chemistry Lab E...
- Microbiology & Pharmacology La...
- D Pharmacy equipment
- B pharmacy Equipments
- Pharmaceutics Laboratory Equip...
- Pharma Analysis Laboratory Equ...
- Animal House lab Equipment
- Pharmacognosy Laboratory Equip...
- Pharmacy laboratories equipmen...
- DEPARTMENT OF PHARMACOLOGY Equ...
- DEPARTMENT OF PHARMACOGNOSY Eq...
- DEPARTMENT OF P'CEUTICAL CHEMI...
- DEPARTMENT OF P'CEUTICS Equipm...
- PHARMACEUTICAL BIOTECHNOLOGY E...
- Livestock & Production Managem...
- Veterinary Sciences Lab Produc...
- Live Stock & Production Manage...
- Genetics and Plant Breeding la...
- Biotechnology lab equipment
- Seed Technology Lab Equipment
- Genetics and Plant Breeding la...
- Biotechnology
- Seed Technology
- Soil Science & Soil Water Cons...
- Entomology Lab equipment
- Agronomy Lab Equipment
- Metrological Lab Equipment
- Plant Pathology & Microbiology...
- Dental Equipment
- Microbiological Diagnostic Equ...
- Industrial & Soil Equipment
- Accessories
- Mega Offer
- Offer Zone
- Tiles Ceramic Laboratory Equip...
- analytical lab Equipment
- ayurvedic drug testing laborat...
- ayurvedic pharmacy instruments
- herbal testing laboratory
- mushroom lab Equipment
- lab plasticware
- agriculture Lab Equipment
- Agriculture College Lab Equipm...
- Labpro Banner 60%
- Labpro banner
- physics 60% Discount
- Hospital equipment supplier Ne...
Top Suppliers
Blog Posts
- green laser Light...
- Student Stereo Mi...
- Binocular Microsc...
- Laboratory Equipm...
- Prokaryos lab and...
- Pharmacy Lab
- Micro lab Laminar...
- MILK TESTING EQUI...
- Micrometer
- Centrifuge Machin...
- Chemistry Lab Equ...
- Agricultural coll...
- full body sanitiz...
- hydrometer for wi...
- Portable Bottle f...
- Egg Incubator
- Laboratorydeal of...
- A complete list o...
- different types o...
- Uses of Microscop...
- Tags: 20 laboratory apparatus and their uses 35 laboratory apparatus and their uses Actuators Analytical Instruments apparatus used in chemistry lab basic laboratory equipment biology lab equipment list pdf chemistry instruments names chemistry lab equipment list pdf chemistry lab equipment near me chemistry lab instrument name chemistry laboratory apparatus and their uses with pictures pdf chemistry laboratory equipment list pdf common laboratory apparatus Communication Networks Control Valves Data Historians Distributed Control Systems (DCS) equipment for laboratory Human-Machine Interface (HMI) Industrial Automation Equipment Industrial Process Instrumentation lab apparatus and their uses lab equipment lab equipment co lab equipment list lab equipment manufacturers lab equipment manufacturers in india lab equipment names lab equipment names and pictures pdf lab equipment names and uses lab equipment near me lab equipment shop near me lab equipment store near me lab equipment suppliers lab equipment suppliers near me lab instruments name lab instruments name list lab tools laboratory apparatus laboratory apparatus and their uses laboratory equipment laboratory equipment and their uses laboratory equipment list laboratory equipment list pdf laboratory equipment manufacturers laboratory equipment manufacturers in india laboratory equipment names laboratory equipment near me laboratory equipment shop near me laboratory equipment stores laboratory equipment stores near me laboratory equipment suppliers laboratory equipment suppliers near me laboratory instruments and their uses with pictures laboratory instruments name laboratory machines laboratory tools pathology lab equipment list pdf Process Control Engineering Equipment Process Control Equipment Suppliers Process Monitoring and Control Equipment Programmable Logic Controllers (PLCs) science equipment store near me science lab equipment names and pictures science lab equipment shop near me science laboratory equipment shop near me scientific equipment supplier Sensors and Transmitters Supervisory Control and Data Acquisition (SCADA) Systems suppliers of lab equipment top 10 laboratory equipment manufacturers in india